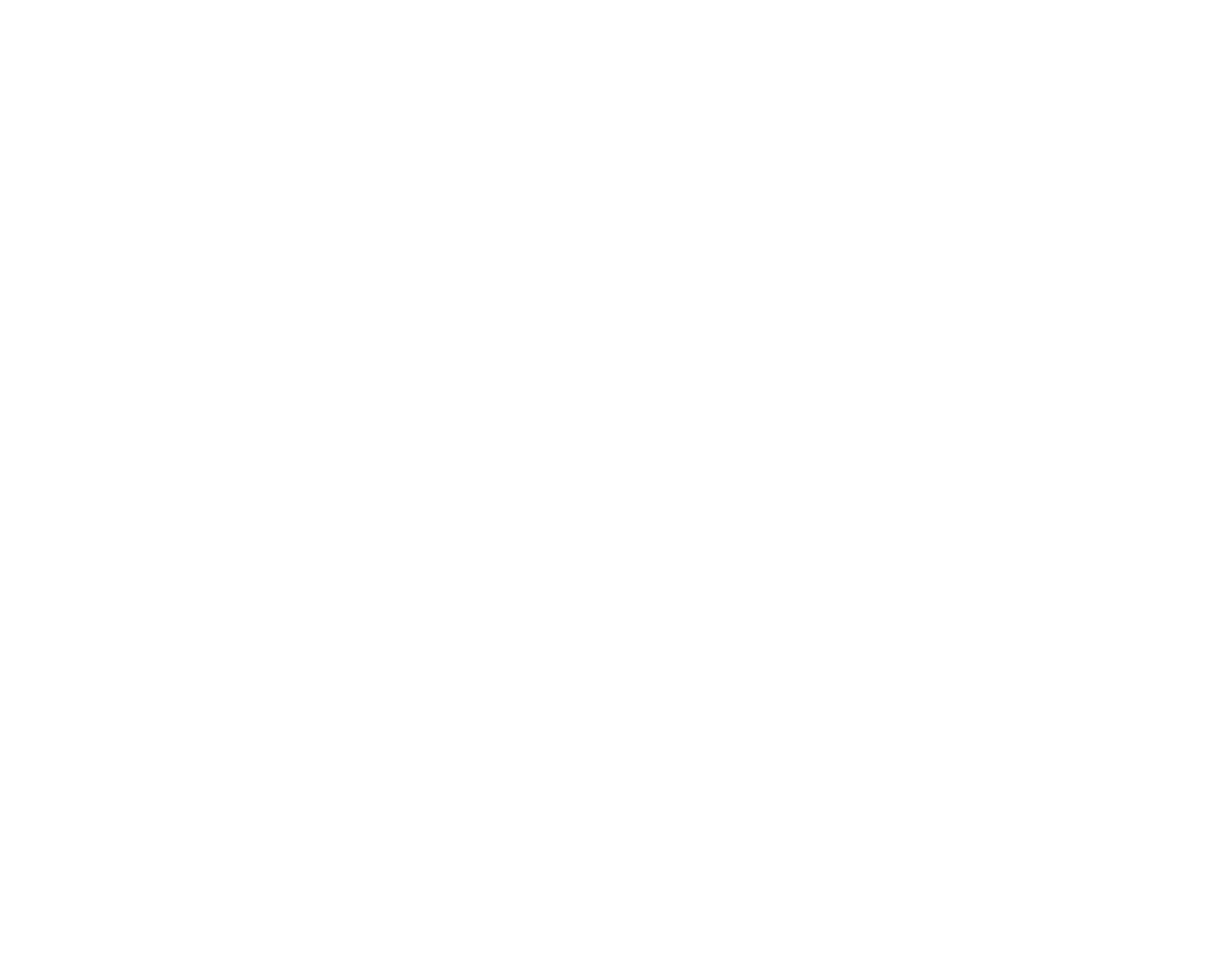
Manufacturers’ training is often designed for heating engineers, but manufacturers are aware of the need for training specifically for electricians. This section aims to highlight the different electrical requirements that each manufacturer, heat pump range, and even individual model may have.
Heat pump data badges provide useful information for heating engineers and electricians, such as:
Heat pumps have traditionally had integrated backup heaters, either within the outdoor monobloc unit or in a separate ‘hydrobox’ which may have a single or multiple stage control. Their capacities and fuse ratings will be displayed on the data badge if installed.
Backup heaters were regularly used to cover part of the annual heat demand but it’s now a requirement that the heat pump should provide 100% of the heat demand at the design outside temperature.
Many heat pumps control the use of the hot water immersion heater, or booster heater as it may be known.
In many heating systems the immersion heater is only used, or primarily used, as part of a regular disinfection cycle (other terms may be used by different manufacturers) to manage the risk of legionella growth. The heat pump’s compressor will raise the stored domestic hot water to a certain temperature (eg 55°C) at which point it will stop and hand over to the immersion heater to take the stored hot water up to a higher temperature for a specified duration. This might be, for example, 60°C for 60 minutes but should be hot enough and long enough to kill any legionella bacteria that might have appeared since the last disinfection cycle. The customer may notice the water’s higher temperature, so it’s always important to discuss the scheduled time and day.
For the rest of the time, the hot water schedule will heat the water to no more than the comfort setpoint – often set to around 48°C. This will be sufficient for all normal domestic uses and can be achieved without the heat pump operating above its optimal range.
For further information on the control of legionella bacteria in water systems, please check – Health and Safety Executive: Approved code of practice and guidance
Some manufacturers of heat pumps use R290 (propane) as the refrigerant. This has a much lower global warming potential (GWP) than other refrigerants but is highly flammable. When R290 units are installed, there will be restrictions inhibiting switchgear within a defined zone surrounding the heat pump. These should be carefully reviewed and complied with where applicable.
Additional requirements may be required where multiple R290 heat pumps are installed together.
Both the latest version of BS7671 and the manufacturer’s instructions should be consulted. Manufacturers have introduced some clarification on the need for the installation of either a type F or type B RCD, based on their testing and in response to MCS and certification body efforts to enforce correct selection. Where no direct current (DC) earth leakage data is given by the manufacturer, best practice is to install a type B RCD.
This is important because the refrigeration system includes two motors and at least two power inverters. As electricity is converted from DC to AC and from AC to DC, some DC current can become present on the earth conductor through leakage. There’s the potential for this DC current to ‘blind’ type A or AC RCD’s as commonly installed in domestic installations, such that it fails to detect any AC fault current.
Whenever available, follow the manufacturers’ instructions for cable selection. However, it’s important to note that some manufacturers might not specify cables or provide specific cable requirements, or they may recommend cable types that are unavailable in the UK. You will need to run at least one power supply and one data cable. Most manufacturers will give separation distances for these cables, and/or require the use of screened cable instead.
Heat pumps use a control logic known as priority hot water. This means the wiring and often orientation of the motorised valve or diverter valve is different to a typical boiler system. Check with the manufacturer’s instructions. In most cases, the signal for hot water demand will energise the valve and move it until the hot water cycle has completed, at which point the valve will return to the resting position and continue heating operation.
With technology changing constantly, and manufacturers having unique requirements, it’s important to refer to the manufacturer’s instructions or installer reference guide, and to attend in-person training where available. Even apparently small requirements can sometimes have significant consequences for the install. For example, some brands of heat pumps require a small amount of current to flow into the compressor windings for a period before first start, to warm the compressor up. This can take up to six hours and could push back the commissioning of an appliance by a day.